Modellierung der Mikrostruktur von Aluminium-Legierungen
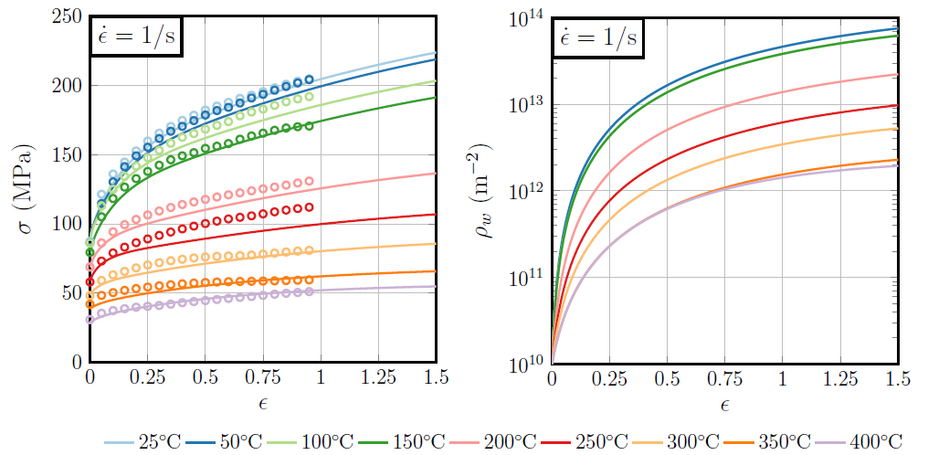
Dabei spielen vor allem Kaltverformung und Rekristallisation, die sowohl Produktionsprozess als auch Materialeigenschaften wesentlich beeinflussen, eine zentrale Rolle.
Aluminium und seine Legierungen sind heute nach Stahl die am zweitmeisten verwendeten Metalle. Vom Transport bis zur Verpackung, in Bauteilen und Fassaden, als dekoratives Element, in der chemischen Industrie oder am Bau – Aluminium ist ein zentraler Bestandteil vieler Anwendungen. Ein Vorteil ist vor allem sein geringes Gewicht bei hoher Stabilität – ein wichtiger Faktor vor allem in der Flug- und Fahrzeugindustrie.
Allzwecklegierungen, die auf dem Al-Mg-Si-System basieren wie 6082, sind für gewöhnlich als Blech oder extrudiertes Produkt zu finden. Sie werden in einer Folge von thermomechanischen Produktionsschritten hergestellt und exakt nach den gewünschten Produktmerkmalen designt.
Obwohl das Design technologischer Legierungen immer noch experimentell ist, können numerische mikroskopische Modelle viele Erkenntnisse über die Beziehung von Mikrostruktur und makrostrukturellen Eigenschaften liefern. Auf diese Werkzeuge sind Industrie und Forschung immer stärker angewiesen.
Kaltverformung
Während des Walzvorgangs verfestigt das Walzgut zunehmend. Der Walzendruck muss daher kontinuierlich erhöht werden, um das Material weiterzuverformen. Dieses physikalische Phänomen, auch Kaltverfestigung genannt, entsteht durch die Zunahme mikrostruktureller Defekte im Material, die während der plastischen (= bleibenden; im Gegensatz zur elastischen) Verformung auftreten. Berücksichtigt man nun die Mechanismen, bei denen kristalline Linienfehler – sogenannte Versetzungen – sich multiplizieren und auslöschen, dann ist es möglich, Stoffmodelle zu designen, die die Änderung der Fließspannung – also die Kaltverfestigung – eines Materials mit seinem mikroskopischen Zustand in Verbindung setzen.
Rekristallisation
Die akkumulierten Defekte in der Mikrostruktur – Versetzungen und Grenzflächen – erhöhen die im Material gespeicherte Energie. Beim Aufheizen werden von Diffusion kontrollierte Mechanismen initiiert, die zur Erholung der kristallinen Struktur und einer Energieabnahme führen. Ist die Glühtemperatur hoch genug, können neue, defektlose Kristalle in hochverformten Regionen nukleieren und in die deformierte Matrix hineinwachsen – dieses Phänomen wird Rekristallisation genannt. Die Korngröße der neu entstandenen Kristalle hängt vom vorangegangenen Deformationslevel ab.
Teilweise rekristallisierte Mikrostruktur nach Plain-strainVerformung bei Raumtemperatur und Glühung bei 300 °C für 20 Minuten. Die Region mit hohem Verformungsgrad rekristallisiert als Erstes.
Das heißt: von der im Material gespeicherten Energie, der Glühtemperatur und von Ausscheidungen einer zweiten Phase, die in der Mikrostruktur vorhanden sind.
Der Einfluss der Erholung ist nicht zu unterschätzen und muss gewissenhaft in jedes Rekristallisationsmodell eingearbeitet werden. Ein solches Modell enthält für gewöhnlich eine Avrami-Gleichung, die, wenn sie mit einem maßgeschneiderten Keimbildungsmodell kombiniert ist, die Rekristallisationskinetik vorhersagen kann. Die Korngröße vorhersagen zu können, ist eine wichtige Erkenntnis für jeden Hersteller. Sie hat direkte Auswirkungen auf die Materialeigenschaften – wie die Festigkeit, die Atomdiffusion oder die Rissausbreitung.
Mehrskalenmodellierung
Ein großes Anliegen der Industrie ist es, die Produktionsprozesse auf verschiedenen Größenskalen darzustellen. Klassischerweise ist ein Finite Element Model gut geeignet, um die makroskopische Skala abzudecken. Integriert man die konstruktiven und Rekristallisationsmodelle mikroskopischer Vorgänge, kann man die verschiedenen thermomechanischen Schritte im Produktionsprozess einer metallischen Platte verfolgen. Beispielsweise ist es möglich, den aus einem Deformationsprozess resultierenden Spannungszustand oder die resultierende Korngröße bei kontinuierlicher Glühung bei 550 °C zu berechnen.
2D-FE-Modell des Walzprozesses mit dem konstitutiven Modell.
Diese Projekt wurde in Kooperation mit der AMAG rolling Gmbh, der TU Wien und dem Austrian Institute of Technology durchgeführt.
Finanzielle Unterstützung kam von der Österreichischen Bundesregierung (im Speziellen vom Bundesministerium für Verkehr, Innovation und Technologie und vom Bundesministerium für Wissenschaft, Forschung und Wirtschaft), vertreten durch die Österreichische Forschungsförderungsgesellschaft mbH sowie der Steirischen und der Tiroler Landesregierung, vertreten durch die Steirische Wirtschaftsförderungsgesellschaft mbH und die Standortagentur Tirol, innerhalb der COMET-Programme.
Korngrößenverteilung in der Dicke der Platte nach einer Glühung bei 550 °C für 20s (in µm).