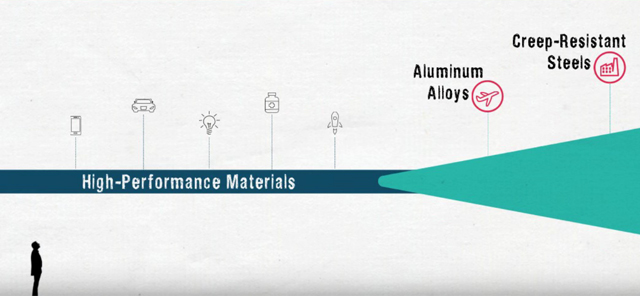
Mission and Vision
"Passionate Lecturers and Researchers" - As a result of our high teaching standards coupled with the external funds we acquired, we have gradually created an exciting and stable working environment
to our actual REPORT ...Visiting Professor Surya D. Yadav from Indian Institute of Technology (Banaras Hindu University), Varanasi and an Alumnus of the TU Graz, hold his lecture on Green Steel: New Challenges. In the picture with students of Advanced Materials Science and host Prof. Cecilia Poletti.
We are honoured to welcome him and grateful for the enriching academic exchange.
We are proud to announce that Lisa Minkowitz has been awarded the prestigious Franz-Leitner-Preis 2025 for the best Master's thesis, sponsored by voestalpine Böhler Welding. ASMET organizes the call for submissions, the review process, and the award ceremony.
Her work explored the AdditiveManufacturing of the AluminiumAlloy AlSi10Mg using LaserPowderBedFusion (L-PBF). By combining ExperimentalDesign with MachineLearning, she modelled the relationship between printing parameters and mechanical properties—ultimately identifying an optimal ParameterWindow for high-performance components. These excellent results were published in Materials and Design (https://doi.org/10.1016/j.matdes.2023.111718).
Her research also included detailed analyses of microstructure, pore characteristics, and heat treatments, culminating in the successful production of a demonstrator for a collector electrode for an ion-engine-driven flying drone! The MSc work was advised by Prof. Sergio Amancio and co-advised by Siegfried Arneitz.
This achievement showcases innovation at the intersection of materials science, data analytics, and aerospace applications – congratulations Lisa!
Our sincere thanks go to voestalpine Böhler Welding for sponsoring the Franz-Leitner-Preis, and to ASMET for their excellent organization of the submission process, expert review, and award ceremony.
We also thank the AustrianResearchPromotionAgency (FFG) for funding the Take Off – FFG projects Ionic Wind Propulsion System for Flying Objects, Part 1 and Part 2, enabling this comprehensive study.
We are very pleased to announce another important and honorable award.
For outstanding international achievements in the science of joining and welding
“Weldability of engineering materials”
given this 28th day of November 2024 by Hidetoshi Fujii, Director of the Joining and Welding Research Institute JWRI, Osaka University
https://www.jwri.osaka-u.ac.jp/en/
The IMAT team personally presented this honorable award to Prof. Cerjak.
Our warmest congratulations!
the winners of the previous year are listed here:
https://www.jwri.osaka-u.ac.jp/work/jwriAward/list/
for the paper "A predictive mesoscale model for continuous dynamic recrystallization" published in the International Journal of Plasticity.
Awarded to Franz Ferraz Miller Branco at the Christmas party, 12 Dec 2024. The the price was taken over by supervisor Cecilia Poletti.
Authors: Franz Ferraz Miller Branco, Ricardo Henrique Buzolin, Stefan Ebenbauer from Voestalpine BÖHLER Bleche GmbH & Co KG, Thomas Leitner from Voestalpine BÖHLER Edelstahl GmbH & Co KG, Alfred Krumphals, Cecilia Poletti
The award-winning publication introduces a mean-field model for thermomechanical processing of titanium alloys. This work emphasizes the interplay between microstructure, flow behavior, and geometry in optimizing thermomechanical processing routes.
Congratulations!
Additional publications related to his thesis:
A comprehensive mean-field approach to simulate the microstructure during the hot forming of Ti-17
Effects of recovery and phase transformation on the recrystallization kinetics of Ti-6Al-4V during β-processing
Metamodelling the hot deformation behaviour of titanium alloys using a mean-field approach
As welding is a significant process in the production of virtually any product ranging from cell phone and computers in the small scale up to transportation, energy production or infrastructure in general, it is evident that is plays a crucial role in a modern society. Knowledge of the basics in materials science and the welding technology is therefore indispensable for companies to develop new products ensuring improvements and maintain competitiveness in a very dynamic market in different industry sectors. Sorin Keller will prove this importance based on his long lasting experience and successful activity for company Alstom on the basis of real cases facing demanding challenges.
Researchers at TU Graz have found a way to strongly join wood with metals and plastics without using glue or screws. This makes wood more usable in cars and planes, offering a sustainable alternative to traditional materials. These methods could be applied in various industries, including automotive, aircraft, and furniture.
video by Birgit Baustädter, Researchers Gean Marcatto and Awais Awan are explaining the joining technique .
By Birgit Baustädter
Using 3D printing technology and ultrasonic joining technique, researchers at TU Graz (Prof. Sergio Amancio, Dr. Gean Marcatto and Awais Awan, PhD) succeeded in attaining an extremely strong joining of the renewable raw material wood with metal and polymer composite. ...
Prof. Sergio T. Amancio Filho has won the prestigious Halil Kaya Gedik Award 2024!
This award is the most important industrial award of the IIW International Institute of Welding. The award is sponsored by Gedik Holding, one of the largest manufacturers of welding consumables in Europe. Prof. Amancio won the Halil Kaya Gedik Award 2024 for his contribution to the education and training of young people in welding and additive manufacturing. This is not only a great personal achievement for Prof. Amancio, but also for the Austrian welding and additive manufacturing community and Technische Universität Graz !
We congratulate Sergio Amancio on this great achievement!
“Injection overmolded lighweight polymer/metal hybrid structures”
The hybridization of polymers and metals has emerged as an innovative and promising approach from technical, economic, and environmental perspectives for obtaining hybrid structures endowed with synergistic properties of their constituents, including mechanical strength, lightness, design flexibility, and chemical durability. These hybrid structures are gaining traction, particularly in the transportation sector, and hold promising applications in the biomedical sector. In this talk, we will delve into recent scientific studies we have performed in this domain, focusing on topics such as processing, microstructure, and mechanical properties of polymer-metal hybrid structures fabricated using the injection overmolding technique.
lecturer: Prof. Leonardo Bresciani CANTO
from Universidade Federal de São Carlos - UFSCar, Departamento de Engenharia de Materiais - DEMa
Award for the paper with the highest impact factor of all the publications produced by the Institute of Materials Science and Welding.
IMAT Best Paper Award 2023 awarded to Dr. Wilian Carvalho for the paper:
"Joining of additively manufactured fiber-reinforced thermoplastic and metals by ultrasonic energy: Mechanical and corrosion behavior"
Willian Sales de Carvalho*, Guilherme S. Vacchi, Carlos A.D. Rovere, S. T. Amancio-Filho
in Materials & Design, volume 234, 2023
https://doi.org/10.1016/j.matdes.2023.112342
Congratulations!
In his guest lecture at Graz University of Technology, Dr. Mario Boccalini, Researcher at IPT – Instituto de Pesquisas Technologicas / Institute for Technological Research in Brazil, will first give a brief overview of the work portfolio at IPT. He will talk about Advanced Materials and their Technological Axes. Also, he will show examples of past and further research projects as a starting point for discussing possibilities of collaborative work with TUGraz.
Wie einfach man Prüfungsfragen verwalten und Prüfungsbögen erstellen kannst, zeigen wir in diesem kurzen DEMO-Video
Das ProjektTEAM:
IMAT: Sebastian Fritsche, Norbert Enzinger, Daniel Radowski
IME: Stefan Kollegger, Michael Bader, Emre Enis Ketan
IIM: Matthias Wolf
LLT: Maria Haas, Josef Wachtler
Weiterführende-Links:
E-Poster
Digitale TU Graz Marketplace
A large amount of the engineering work for the aircraft structure development is related to fatigue and damage tolerance. In the lecture, first a short overview of the fundamentals of fatigue and fracture mechanics disciplines will be presented. Lessons learned from the past will help to explain the evolution of philosophies for fatigue evaluation, from safe-life to fail-safe, and then to damage tolerance. The present fatigue and damage tolerance requirements will be also discussed in short.
It can be said that the aviation and mobility industries is experiencing a revolution period in terms of new technologies. The lecture closes with an overview of future challenges on the development of aircraft structures, such as damage tolerance for composite and hybrid structures, new materials, additive manufacturing, smart structures, and others.
The above topics will be addressed by Dr. Carlos Chaves, Principal Structures Engineer at Embraer, in his guest lecture at Graz University of Technology.
One characteristic of the gas and steam turbines built since 1929 by BBC / ABB / Alstom and today GE is that the rotor is welded from individually tempered forged components. With more than 89 years of experience with welded rotors for steam turbines, gas turbines and turbogenerators, GE has successfully welded together more than 7800 turbine rotors. Rotor welding technology can also be used to repair damaged rotors of any type if welding is possible.
In his guest lecture at Graz University of Technology, Sorin Keller, Manager Welding & Brazing Technology – GE Power Switzerland and President of the International Institute of Welding, talks about past developments and future challenges.
A major challenge in future will be to reliably weld established and new materials. The focus is on rationalising welding processes to increase the efficiency of power plants and thus make a lasting contribution to protecting the environment.
Emir Hodžić was awarded the AMAG Innovation Prize in the category Best Paper "technological" on April 26, 2023 at the "AMAG Innovation, CIP and Social Award Presentation 2023" event for his publication:
"Influence of alloy composition and lubrication on the formability of Al-Mg-Si alloy blanks" in the "Journal of Manufacturing Processes" as part of his PhD thesis and was recently presented by Dr. Werner Fragner, Head of AMAG Corporate Technology.
Congratulations!
Prof. Sergio Amancio was honored with the prestigious Yoshiaki Arata Award 2023.
This internationally renowned prize of the IIW International Institute of Welding is awarded for outstanding achievements in basic research in welding and joining technology.
Prof. Sergio Amancio was presented with the award at this year's IIW ANNUAL ASSEMBLY AND INTERNATIONAL CONFERENCE ON WELDING AND JOINING in Singapore.
Congratulations!
We are also very pleased that our institute can thus present two winners of the ARATA Award. Emeritus Prof. Horst Cerjak was honored for his achievements in 2007.
THERMEC’2023, the world largest international conference on the Processing & Manufacturing of Advanced Materials, was jointly organized by IMAT/TU Graz and WWT/TU Wien in Vienna from July 2 – 7, 2023. It was the twelfth international conference on advanced materials upon the proven concept that continues the tradition of its
predecessors: virtual conference (2021), Paris/France (2018), Graz/Austria (2016), Las Vegas/USA (2013), Canada (2011), Germany (2009), Canada (2006), Spain (2003), pUSA (2000), Australia (1997) and Japan (1988).
In Vienna, Thermec attracted over 1150 delegates from 40 countries around the globe in the field of advanced materials and manufacturing technology representing universities, government research labs and industrial organizations. More than a fourth of the participants came from Japan, followed by the countries with the most participants: South Korea, Germany, Austria, France, and The People’s Republic of China.
The conference covered all aspects of processing, fabrication, structure/property evaluation and applications of both ferrous and non-ferrous materials, composites including biomaterials, fuel cells/hydrogen storage technologies, batteries, super capacitors, nanomaterials for energy and structural applications, aerospace structural metallic materials, bulk metallic glasses, and other advanced materials.
The plenary lectures were given by Terry Langdon from University of Southampton/UK and Prof. Tadashi Furuhara from Tohoku University, Japan.
The conference was held at TU Wien.
Two workshops have been organized in front of the conference: „Advanced steel – microstructure design, characterization, and modeling”and “Aluminium Alloys”.
The Conference dinner, together with the distinguished THERMEC award ceremony, was hosted by ACV – Austria Center Vienna. The dinner was accompanied by the “Swobodas Swing Trio”.
Special thanks go to the sponsors voestalpine, AMAG, MatCalc, and the Mayor of Vienna. In addition, our exhibitors Dynamic Systems Inc (DSI)/USA, Trans Tech Publications/Switzerland, PULSTEC Industrial Co.Ltd/Japan, ThermoCalc/Sweden, MDPI, PR China/Spain, MatCalc Engineering/Austria, Zeiss Microscopy/Austria, Matplus GmbH/Germany, SURFACE systems/Germany played an important role so that the Conference Organizers have received very positive feedback from participants from all over the world.
Thermec’2023 conference was a great success and we received very good feedback and acknowledgment.
The next Thermec conference will be held in Tours in France in July 2025.
listen to our new podcast episodes at the TU Graz channel:
https://www.tugraz.at/en/tu-graz/services/news-stories/talk-science-to-me/all-episodes
"Smart Products from Smart Factories"
If we think today about the factory of the future, robots, artificial intelligence, resource-efficient production methods and new materials have a firm place in it. At TU Graz, research is being carried out o turn this vision into reality.
Interviews by Birgit Baustädter:
podcast#6 Christof Sommitsch on smart production.
podcast#7 Franz Haas on future production
podcast#8 Rudolf Pichler the smartfactory@tugraz
podcast#9 Sergio T. Amancio Filho on new joining techniques
Printversion: TU Graz research#28
We are very honored that this year two prestigious prizes from the Deutsche Gesellschaft für Materialkunde e.V. (DGM) were awarded to our institute.
The presentation of the awards took place at the DGM Day on September 26, 2022 in Darmstadt.
Every year, the DGM awards the "DGM Young Investigator Award" to doctoral students or postgraduates in the field of materials science and materials engineering for the above-average study and work results of four talented young researchers.
Laudatio for Dr. techn. Ricardo Henrique Buzolin
The DGM Prize is awarded to an excellent mid-career scientist for outstanding scientific or scientific-technical achievements that represent a breakthrough in materials science and engineering documented by publications or have opened up a new field of research.
... The German Society for Materials Science e.V. awards Univ.-Prof. Dr.-lng. Sergio Amancio the DGM Award 2022 for his fundamental and innovative contributions to nanomechanics and plasticity of complex materials.
Materials engineer and materials scientist Univ.-Prof. Dr.-lng. Sergio Amancio has been working on the materials science and manufacturing processes of metal-fiber composite hybrids since the early 2000s. The focus of his highly successful research career has been on the development of more energy efficient as well as effective joining and additive manufacturing processes for hybrid materials. For his extensive engineering achievements, Prof. Amancio has been recognized not only by the scientific community but also by the industry with over 100 Scopus-referenced publications, 22 patent grants and 17 awards. These outstanding achievements, which Sergio Amancio can already show in the middle of his research career, point to a promising scientific future and make him an outstanding candidate for this year's DGM Award.
Laudatio for Univ.-Prof. Dr.-Ing. Sergio Amancio
published by Elsevier / Woodhead Publishing
Authors: Sachin Salunkhe, Sergio T. Amancio-Filho and J. Paulo Davim
The new book provides fundamental information and the latest research on metal additive manufacturing technologies, including powderbedfusion, direct edenergy deposition using high-energy beams, and hybrid additive and subtractive methods.
We would like to thank all book chapter authors for their valuable contribution to this project. A special thanks to Rafael Paiotti from our institute, who led the preparation of two excellent chapters (Chs. 1 and 2) with the participation of University of Applied Sciences Upper Austria and JOANNEUM RESEARCH Forschungsgesellschaft mbH.
Save the date:
September 1, 2022, 2 p.m., lecture room E, Kopernikusgasse 24/I
As the Welding Engineering undergraduate programme at The Ohio State University (OSU) is completing 75 years in 2023, it has evolved to become a key player in the education and research on materials joining within the U.S. and across the world. In 2010 OSU joined efforts with the U.S. National Science Foundation (NSF) and other key universities across North America to establish the Manufacturing and Materials Joining Innovation Center (Ma2JIC). This center has brought together researchers from seven different universities in U.S. and Canada and more than 60 industrial and government organisations from around the globe to cooperatively develop state-of-the-art and economically relevant research on materials joining and metal additive manufacturing (AM), totaling more than US$50M. Today Ma2JIC invests $5.5M per year to support approximately 30 different research projects, which involve about120 researchers and students across The Ohio State University, University of Tennessee-Knoxville, Pennsylvania State University, Colorado School of Mines, and the University of Waterloo.
In his Guest Lecture, Antonio J. Ramirez from Ma2JIC will present highlights of the research and technologies developed by OSU and Ma2JIC, ranging from fundamental studies on solidification cracking during welding and Additive Manufacturing, powder- and wire-based metal AM, and conventional welding processes like friction stir welding and resistance spot welding of advanced steels and dissimilar materials.
About Antonio Ramirez
Antonio Ramirez from the Ohio State University (OSU) – which is the top ranked university in welding and joining in the US) – is an expert in Metal Additive Manufacturing and solid-state welding processes and director of the Ma2JIC center.
We are pleased to announce another great award.
Florian Pixner was awarded the "Welding in the World Best Paper" sponsored by the IIW International Institute of Welding at the 75th IIW Annual Assembly in Tokio 2022 http://www.iiw2022.com/
in the Category A: Welding Processes and Additive Manufacturing in Recognition of his outstanding research paper:
Contactless temperature measurement in wire-based electron beam additive manufacturing Ti-6Al-4V
Co-authors: Ricardo Buzolin, Sebastian Schönfelder from pro beam additive GmbH, Gilching, Germany; David Theuermann, Fernando Warchomicka and Norbert Enzinger.
We are happy to announce our award at this year's Energie Globe Award Styria 2022.
The project team at IMAT, Willian Carvalho, Carlos A. Belei and Prof. Sergio T. Filho Amamcio, BMK Endowed Professorship for Aviation and head of the institute Prof. Christof Sommitsch was awarded for the project: "GreENJOINable - Enabling next-generation green aircraft structures" in the research category and is nominated for the international Energy Globe Award in the AIR category.
Content: Innovative composite materials and efficient ultrasonic joining technology reduce CO2 emissions through lower aircraft weight.
to the award:
http://www.news.steiermark.at/cms/beitrag/12879196/154271055/
http://www.energyglobe.at/ueber-energy-globe
After receiving our new welding machine in April, we were now able to carry out the official introduction and demonstration by Matthias Moschinger followed by a celebration.
Head of the joining group is Norbert Enzinger: "SBI M3DPSL plasma welding unit with multiple filler material input options opens a whole range of new possibilities.
Guest lecture "Welding and repair solutions for damaged large components in turbomachinery".
Sorin Keller, President of IIW (International Institute of Welding) and Manager Welding & Brazing Technology, GE Power.
Save the date:
27th of April 2022, at 13:00 in the lecture room A, Kopernikusgasse 24/I
GE has many years of experience with welded rotors for steam, gas turbines and turbogenerator rotors. From 1929 to the present, more than 7,800 rotors have been manufactured from identical materials or different combinations of materials. The future challenge lies in mastering the welding technology on new materials, as well as in further optimizing and streamlining the welding processes, with the aim of increasing the efficiency of the power plants. The greatest challenge lies in the development and implementation of repair processes that ensure the operation of these machines to a modern environmentally friendly standard, thus making a sustainable contribution to the conservation of resources and the environment. In the context of these developments, failure analysis is an essential tool that is used to bring reliable products to market.
for the next ADVANCED MATERIALS POSTER DAY on 22nd of April 2022
submit the abstract of your poster online until 11th of April
A constant motivation in aeronautical engineering is the research of new materials that enable the weight reduction of flying objects without reducing their strength and thus effectively decrease their fuel consumption. However, since most of today’s commercial airplanes and helicopters are powered by fossil fuels, a reduction of the CO2 emissions towards zero is not possible. Therefore, another research focus is looking at the development of alternative propulsion systems that can reduce CO2 emissions even further and thus effectively counteract future climate changes.
In the course of the FFG-funded project IonAs, an all-electric propulsion system powered by ion wind was studied by IMAT in cooperation with the IHS (Institute of High Voltage Engineering and System Performance – TU Graz) and the IAV (Institute of Aviation – FH-Joanneum). Due to the fact that such ionic wind powered systems provide much lower thrust than conventional systems, weight reduction is even more important. This goal can be achieved by combining lightweight materials and additive manufacturing (in this case Laser – Powder Bed Fusion), which enables the production of highly complex parts that cannot be manufactured in any other way.
In this project, the team has successfully manufactured a hybrid demonstrator in the shape of an air foil that consists of two parts: The front part was additively manufactured with the use of AlSi10Mg alloy and shows the possibility of printing small structures of 200µm in thickness. The rear part of the air foil was made out of CFRP (Carbon Fibre-Reinforced Polymer) and was manufactured by the colleagues of IAV. Due to the great outcomings of this project, the follow up FFG-project IonAs² was approved and is already running, including two additional project partners (Institute of Fluid Mechanics and Heat Transfer – TU Graz and Institute of Electrical Measurement and Sensor Systems – TU Graz), with the aim to bring the idea of flying with the power of ions to a new level!
On the occasion of the event "From Science to Innovation" on 9th of November at the Karl-Franzens University the Technische Universität Graz honors its inventors.
The award "Inventor of the TU Graz" was given to Sergio T. Amancio Filho, Christof Sommitsch, Pedro Effertz and Mohammad Reza Ahmadi (from left to right) for their groundbreaking inventions in the field of materials science.
Mr. Dipl.-Ing. Matthias Moschinger, IWE and university project assitant at the IMAT Institute, has received the “Richard Marek Award 2021” for his article „Elektronenstrahlschweißen dünnwandiger Aluminium Liner“ Congratulations!
The award was handed over by the speaker of the presidium of the ÖGS, Mr. Guido Reuter. The prize was given for innovative solutions in welding technology.
The HPS students managed again, after an exciting overtaking jad before the last stroke, with only a distance from 0.2 nautic miles but with a 30-minute lead over the second-place finisher in the home stretch, after a continuous 3-day race over the distance of 370 nautical miles in the class B46.
https://roundpalagruza.at/rpc-2021-wertung-bavaria-46/
Our Congratulations to the High Performance Sailing HPS Students Team of TU Graz:
Felix Meixner from IMAT, Tobias Wöhr, Jakob Fuchsberger, Bernhard Golser, Michael Kolm, Jakob Kreisel, Valentin Leutgeb and Vincent Philipp
Guest lecture "Welding and Brazing technology, as key processes in the manufacturing of power generation components" Sorin Keller, IIW president and Manager Welding & Brazing Technology, GE Power on
virtual:
Our AddLab was presented during the 11th Conference of Learning Factory on 1-2 July 2021 in Graz.
Peter Steinkogler, multiple state champion in various boat classes, designed a revolutionary sailboat concept, not only as a record-breaking sailboat, but especially how a sailboat could function most economically and effectively. - This especially for possible implementations for zero-emission cargo sailboats.
IMAT and furhter institutes at TU Graz were partners in the development of the V_REX in the fields of avionics, sensor technology, materials science, fluid mechanics, optimization and modeling.
At IMAT, bachelor theses for the finite element calculation of the hydrofoils as well as the production of the boat models for tests, which is now being put into action and can be actively supported via Kickstarter.
Projekt Partners and Institutes at TU Graz:
Univ.-Prof. Siegfried Vössner, Institute of Engineering and Business Informatics
Univ.-Prof. Franz Wotawa; Institute of Software Technology
Assoc.Prof. Walter Meile; Institute of Fluid Mechanics and Heat Transfer
Student Projects at IMAT:
Poster: New concept highspeed sailing boat – model setup and wind tunnel test
H. Pardatscher1, C. Resch1, P. Steinkogler2, W. Meile3, L. Weingrill1 and C. Sommitsch1
Das Programm zur 15. Werkstofftagung steht unter dem Motto "Additve Fertigung von performanten und hybriden Strukturen" und ist online verfügbar. Weitere Informationen zur Anmeldung und zu unserem Sponsoringangebot finden Sie unter
We welcome Prof. Herman Nied, Professor at the Department of Mechanical Engineering & Mechanics at the Lehigh University, Pennsylvania U.S. at Graz University of Technology.
Prof. Nied was selected for a Fulbright Award to Austria by the J. William Fulbright Foreign Scholarship Board, a presidentially appointed 12-member board. The Fulbright Program is one of the most important and prestigious international educational exchange program of the United States.
Since 2009, several Fulbright Professors have been active in reserach and teaching at Graz University of Technology and we are proud to announce our first fulbright professor at IMAT for this summer term 2021.
During his stay, Professor Nied will be holding two courses:
Gastvortrag "Behebung von Schäden an Dampf und Gasturbinen -Rotoren durch Schweissen" von Hr. Dr. Sorin Keller, Manager Welding & Brazing Technology, GE Power am
Montag, online am 08.03.2021 14:15 - 17:15 Uhr
https://tugraz.webex.com/tugraz-de/j.php?MTID=m0e6ad3b8730597aa1ac4bfc642e55351
The development of structural shape-memory alloys dates back the 1940s and 1950s, being the most employed alloy the well-known Nitinol (or NiTi). Due to the shape memory effect, these functional metals have the ability to be deformed and recover their shape when heated. In a nutshell, these functional effects deliver high stresses, therefore enabling Nitinol to be used as an actuator. However, their use in main stream functional-structural applications has been somehow hindered mainly to their complex processing, machining, and high reactivity. Additive manufacturing has the potential to mitigate these drawbacks, as near-net shape parts can be produced with lesser manufacturing steps and higher materials savings. In our recent publication https://doi.org/10.1177%2F1464420720975059 we have shown that NiTi alloys can be successfully additively manufactured with electron beam free forming fabrication (EBF3), also known as wire-based electron beam additive manufacturing (w-EBAM). The project has been led by Rafael Paiotti, project assistant and PhD candidate at BMK Endowed Professorship of Aviation in close collaboration with Florian Pixner from the Joining Technology group Printed parts were tested in cooperation with Institute for Chemistry and Technology of Materials, under ad-hoc consultancy of Embraer.
Contact: Univ. Prof. Dr.-Ing. Sergio Amancio
The best students are in great demand at all institutions in order to collaborate in research projects as well as in teaching. As a consequence, the ESP – IMAT Elite Student Programme for Materials Science, Joining and Forming was launched in the academic year 2016/17 to enable high-potential students to be in an interesting programme. We welcome our new Elite Students for the academic year 2020/21.
Vienna, 9/26/2020
The 1st Meeting of the Brazilian Scientific Diaspora was held on 9/26/20, in Vienna, with the presence of the Minister of Science, Technology and Innovations, Mr. Marcos Pontes, the Ambassador of Brazil in Vienna, José Antônio Marcondes de Carvalho, and 21 researchers, residing in Austria and Slovakia. The meeting was opened with the words of the Ambassador of Brazil to Austria, which was followed by a speech by Minister Marcos Pontes and interactive debate with members of the diaspora. In his opening speech, Ambassador Marcondes highlighted the importance of observing the phenomenon of emigration of qualified professionals from the perspective of networks formed by researchers, instead of a concept exclusively of “brain drain”. He noted the diversity of present researchers, coming from different regions of Austria, and with different areas of expertise. The Brazilian Ambassador stressed the fact that ‘Brazil is an innovative and creative country’ and mentioned ‘the mobilization of Brazilian scientific diasporas abroad as one of the main tools to increase the scientific and technological cooperation between Austria and Brazil.’
Minister Marcos Pontes – an engineer and retired NASA astronaut - welcomed the organization of the meeting of the Brazilian scientific community in Austria, highlighting the importance of technology in human development and the fundamental role played by science, technology and innovation. Following topics were discussed in this meeting: (a) exchange of Brazilian and Austrian students, by supporting partnerships between research and teaching institutions in both countries; (b) identification of new R&D trends in Austria as a way to contribute to the establishment of new topics in Brazil; (c) Creation of an association for the Brazilian diaspora in Austria to foster the above-mentioned topics.
Marina Melo Gontijo, Willian Sales de Carvalho and Prof. Sergio Amancio (in the picture with Minister Marcos Pontes) had the honor of representing TU Graz and IMAT in this important event. Prof. Amancio had the chance to discuss current and future developments in the field of materials science and manufacturing with Minister Pontes.
Prof. Sommitsch is Speaker at the 11. Ranshofenener Leichtmetalltage
The widely known and respected newspaper “Der Standard” publishes weekly a portrait of a young talent from science in the column called “Geistesblitz”. Researchers working in Austria are interviewed and invited to tell about their work, motivation and a small personal insight.
Marina Gontijo, one of the PhDs at IMAT, was invited to share about her work in this column, published on the 4th of March.
The publication of IMAT team brings new insight to the successful printing process of the neodymium-based magnets.The paper describes in an detailed way behaviour of the material molten by laser and its influence on the final magnetic properties of a 3D printed component.
published:
One step closer to effective 3D printing of super-strong magnets. The team of IMAT / TU Graz researchers developed an effective 3D printing process of NdFeB magnets. Next goal is to translate the lesson learned to another promising material: FeCrCo.
more arcticles:
The Chamber of Commerce of Styria awarded the WKO Research Promotion Prize to 19 fellows and institutes this year. Mr. Anto Zelic received for his outstanding master’s thesis, which he carried out at our IMAT institute and under the supervision of Mr. Florian Pixner, the research prize of EUR 2,100 that was given by Mr. Josef Herk, President of the Chamber of Commerce of Styria on December 4, 2019 as part of the official grant ceremony. In total there were 5 scholarship holders from TU Graz.
We congratulate quite cordially!
Link zum Video:
The AddLab@tugraz has recently started as cooperation between the two institutes IMAT (Institute of Materials Science, Joining and Forming) and IFT (Institute of Production Engineering) in the area of metal additive production using selective powder printing techniques. Currently two printers are available:
It is planned to extend together the AddLab@tugraz regarding technologies and materials
The international student project marathon was a cooperation between Peter the Great St. Petersburg Polytechnic University (SPbPU) and Graz University of Technology. The IMAT was involved in two out of six projects.
The 14th Materials Day of the Institute of Materials Science, Joining and Forming of Graz University of Technology took place on November 28, 2019 and focused on innovative solutions in modern joining technology. In the beautiful assembly hall, Rector Prof. Harald Kainz welcomed around 130 participants coming from science and business, among them selected students of the vocational education and training college – HTL Mödling. In his opening speech, he introduced the impressive development of Graz University of Technology and responded to the contribution on this success of Em.Prof. Horst Cerjak, the person celebrating his big birthday. The head of the institute, Prof. Christof Sommitsch, subsequently paid tribute to his predecessor Em.Prof. Dr.mont. Horst Cerjak on his 80th birthday by pointing out selected contributions from his very fulfilling and and successful professional life. Afterwards Prof. Sommitsch presented an overview of the ongoing and prospective main topics of the institute.
In the first block of the event, two specialist lectures on current research topics were presented. Mr. F. Pixner talked about the wire based additive manufacturing as part of joining technology and Dr. M. Skalon presented the powder bed process, where he focused his lecture on an innovative approach to parameter development of new powders. After the coffee break Prof. G. Wilhelm, who also works for Lorch Schweißtechnik GmbH, introduced his research results of the MSG build-up welding processes of iron-tungsten pseudo-alloys under consideration of the welding process. Mr. E. Wagner focused then on the current situation of the additive manufacturing with electron beam in general and in particular on features at pro-beam GmbH. Ms. A. Putz presented parts of her PhD thesis in the field of flux-cored wire welding of standard duplex steel, notably the very innovative AHT method. After lunch, Mr. Th. Willidal (voestalpine Böhler welding Austria) presented the concept of the flux cored wire in general and in particular the implementation for a nickel-based alloy. Mr. H. Staufer from Fronius International GmbH, demonstrated the possibilities and potential of the laser-MAG tandem hyprid process in terms of the large tolerance to variable gap dimensions. Next, Prof. Amancio presented selected methods for joining dissimilar compounds, paying particular attention to the friction-based processes. The last presentation of Ass.Prof. Domitner focused on the simulation of self-pierce riveting in modern car body construction.
At the end of the seminar guided tours through the labs of the institute were offered. Summing up the Materials Day showed current trends and innovative solutions in modern joining technology from a scientific and industrial point of view and everybody had the chance of interdisciplinary discussions and networking.
On November 7, 2019 Prof. Sergio Amancio delivered his cutting-edge Inaugural Lecture at TU Graz with the title: Flying fast forward: Innovative hybrid materials and manufacturing technologies for aviation. In his talk he addressed the historical aspects of lightweight materials and structures in modern civil aviation and presented the latest developments on manufacturing of lightweight hybrid structures for future airplanes. The focus of Prof. Amancio’s lecture was set on novel joining and additive manufacturing techniques for metals, composites and metal-composite structures.
Mr. Josef Plangger, Master student at the IMAT Institute, has received the this year’s “Richard Marek Award” for his article „Process development for additive manufacturing of a crane component“ within the scope of the fair „Schweissen 2019“ in Linz. Congratulations!
The award was handed over by the speaker of the presidium of the ÖGS, Mr. Guido Reuter. The prize was given for innovative solutions in welding technology.
for the next ADVANCED MATERIALS DAY on 26th of Septmeber 2019
submit the abstract of your poster online until 20th of September
Mateusz Skalon hat ein innovatives Pulver für den 3D-Metalldruck entwickelt und arbeitet nun an dessen Marktreife.
An der TU Graz wurde ein Stahlpulver für die additive Fertigung entwickelt, das die Produktion komplexer Bauteile entscheidend vereinfacht. In einem Spin-Off-Förderprogramm wird nun an der Marktreife gearbeitet.
Kürzere Produktionszeiten, geringere Kosten und weniger Produktionsfehler: Dies sind nur einige Gründe, warum die metallverarbeitende Industrie immer öfter additive Verfahren einsetzt.
Recently the STYRIAM METALS team took part in Fifteen Seconds Festival from 6 - 7 June 2019 in Graz and gave a pitch about the product.
STYRIAM METALS is a start-up team located in Graz (Styria, Austria) at TU Graz working on metallic powders for Additive Manufacturing.
Head of the team is Mr. Mateusz Skalon from IMAT.
The team develops a modification process of steel powders utilised for Selective Laser Melting (SLM). The powder modification allows to eliminate the need of supporting the printed components during the printing process. This extends a freedom of design by enabling a unique feature of horizontal printing without supports. With this unique technology it is planned to enter the rapidly growing market of additive manufacturing.
STYRIAM METALS is an outcome of FFG Spin-Off Fellowship programme: NewGen SLM Powder.
On March 7 2019, the Dörrenberg Studien AWARD was awarded for the 11th time to students, who have studied materials engineering topics such as steel, heat treatment, surface engineering or process engineering.
Ms. Jana Joeressen is one of this year’s award winners!
She was honored for her excellent Bachelor thesis „Corrosion tests on duplex steels“, that she carried out at the IMAT institute in 2018 under the supervision of Prof. Norbert Enzinger, Dipl.-Ing. Andrea Putz and Wolfgang Steinbäck from the corrosion laboratory. Congratulations!
In a press conference on Dec. 12, 2018, the Austrian minister Mr. Hofer (BMVIT) has launched the Research, Technology and Innovation (FTI) Strategic Advisory Board for the Austrian aviation sector. Prof. Sergio Amancio – a member of the board - represents TU Graz in the area of materials and manufacturing technologies.
We would like to inform you about the open acess in the journal "materials"
Deadline for manuscript submission: 1 August 2019
Vienna, 13.09.2018. Prof. Sergio Amancio met the Federal Minister of Transport, Information and Technology, Ing. Norbert Hofer at the official BMVIT Endowed Professorship event introducing the new university professors.
Institute of Materials Science, Joining and Forming
Graz University of Technology
Kopernikusgasse 24/I
8010 Graz - Austria
phone: +43 316 873 7181
fax: +43 316 873 7187
office.imat @tugraz.at
www.imat.tugraz.at