#9: Sergio Amancio
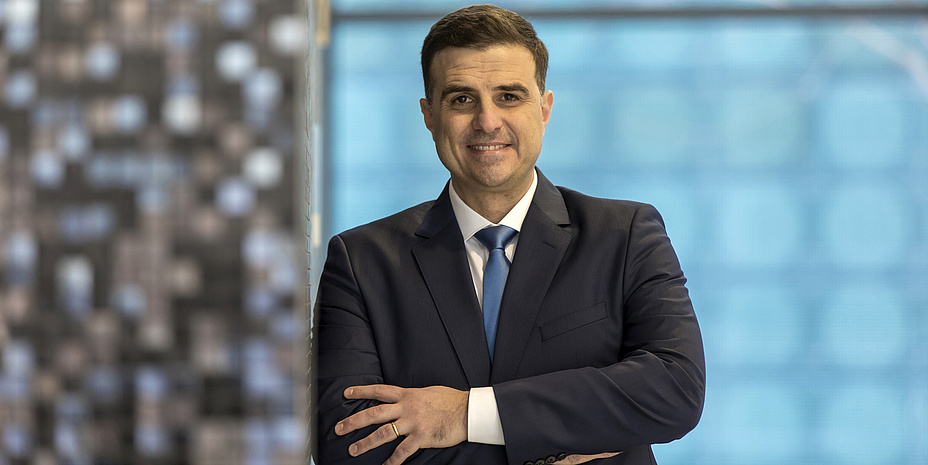
Der folgende Text ist ein wörtliches Transkript der Podcastfolge.
Talk Science to Me – der Wissenschaftspodcast der TU Graz
Hallo und schön, dass ihr heute wieder mit dabei seid. Mein Name ist Birgit Baustädter und ich darf euch durch den Wissenschaftspodcast Talk Science to Me führen. Mein Gast ist heute Sergio Amancio. Er beschäftigt sich vor allem mit neuen Materialien und Produktionsmethoden in der Luftfahrt. Der gebürtige Brasilianer hält mehrere Patente und untersucht vor allem, wie metallische Werkstoffe mit Verbundwerkstoffen gefügt werden können.
Talk Science to Me: Herr Prof. Amancio. Vielen Dank, dass Sie heute meine Fragen beantworten.
Sergio Amancio: Sehr gerne.
Wir haben heute einen wunderschönen Tag an dem wir diesen Podcast, diese Folge aufnehmen. Ihr Büro ist gleich um die Ecke - wie war Ihr Arbeitstag bisher?
Amancio: Grundsätzlich nur Besprechungen (lacht). Sehr spannend. Wie fast jeden Tag, wenn man unterwegs in Besprechungen ist.
Woran arbeiten Sie gerade?
Amancio: Grundsätzlich an der Revision und Korrektur von Manuskripten - akademischen und wissenschaftlichen Manuskripten.
Was die Forschung anbelangt geht es in die Richtung der additiven Fertigung. Das Fügen von Leichtbaustrukturen. Die Verbindungen von Verbundwerkstoffen und Metallen.
Talk Science To Me ist der neugierigste Wissenschaftspodcast der Podcastwelt – aber vor allem der TU Graz. Wir stellen Fragen – unsere Forschenden antworten. Von künstlicher Intelligenz über Nachhaltiges Bauen bis hin zu Mikroorganismen, die sich von CO2 ernähren und so Proteine erzeugen. Hört rein und lasst euch begeistern.
Abonniert die neuesten Folgen auf der Podcast-Plattform eures Vertrauens:
iTunes
Google Podcasts
Spotify
Deezer
Amazon Music
RSS-Feed
Warum ist das so wichtig? Wo wird das eingesetzt?
Amancio: Das ist ein sehr aktuelles Thema, weil die Ersparnis von Gewicht bzw. die Verringerung der Emissionen eine sehr wichtige und sehr große Rolle spielen bei nachhaltigen Anwendungen. Und wir reden über die Anwendung im Bereich Automobilbau, aber auch in der Luftfahrt. Insbesondere in der Luftfahrt, wo meine Expertise, mein Schwerpunkt zu finden ist. Aber diese können sowohl in der Luftfahrt als auch in der Raumfahrt und wie gesagt im Automobilbau, aber auch in der Medizintechnik eingesetzt werden. Das sind mehrere Industriesektoren, die von unseren Ergebnissen, unserer Forschung profitieren können.
Sie haben gesagt, Sie arbeiten daran, dass sich verschiedene Materialien miteinander verbinden können. Unter anderem Kunststoff mit Metall. Was ist daran die Herausforderung? Warum geht das nicht einfach?
Amancio: Genau. Man fragt sich, warum nicht eine Struktur, die metallisch ist oder voll aus Kunststoff oder Verbundwerkstoffen hergestellt wird. Das wäre viel einfacher was die Werkstoffe bzw. die Fertigungstechnik anbelangt. Aber die Herausforderungen der heutigen Autos und Flugzeuge verlangen Mischbaustrukturen - verschiedene Materialien zusammenzufügen. Und wenn man Kunststoff und Metall insbesondere betrachtet: Die sind Stoffe, die sehr unterschiedlich sind, was ihre Struktur und Zusammensetzung anbelangt, im Vergleich mit Metallen. Metalle sind grundlegend kristalline Materialien, haben auf atomarer Ebene eine regelmäßige Struktur. Während der Kunststoff keine so regelmäßige Struktur hat, seine ist zum Teil kristallin und zum Teil amorph. Und in der Praxis, wenn Sie versuchen, sie auf der geschmolzenen Ebene zu mischen, dann verhalten sie sich wie Essig und Öl. Das heißt, sie mischen sich ungerne miteinander. Und deswegen, wenn man sie schweißen oder fügen will mit einer externen Wärme, wie es beim Schweißen zu finden ist, braucht man eine sehr gute Kontrolle der Wärme, also der Temperatur, damit man den Kunststoff, der weniger thermisch beständig ist, durch die Hitze nicht zerstört. Und das ist eine große Herausforderung. Also die geringe Mischbarkeit zwischen Kunststoff und Metall und die thermische Beständigkeit des Materials. Das sind die großen Herausforderungen. Es gibt aber auch die Unterschiede im Ausdehnungskoeffizienten. Das heißt, ein Material dehnt sich aus im Vergleich zu dem anderen. Beziehungsweise ziehen sie sich auch bei der Erstarrung oder Kühlung in verschiedenen Raten zusammen. Das heißt, wenn man Metall zu Kunststoff mit herkömmlichen Fügeverfahren, also Schweißverfahren versucht zu fügen, passieren in der Regel Delaminationen. Das heißt, sie werden voneinander während des Abkühlungsprozesses getrennt, wegen dieser unterschiedlichen Ausdehnungskoeffizienten.
Und warum verwende ich nicht einfach einen sehr starken Klebstoff, um die miteinander zu verbinden?
Amancio: Klebstoff und mechanische Verbindungen, wie Nieten oder Verschrauben sind bis vor Kurzem auch immer die erste Wahl gewesen, auch bei neuen Verbindungen oder bei neuen Strukturen. Allerdings gibt es Limitationen bei Verbundwerkstoffen und Metallen, die heute erforscht werden oder schon in einer Anwendung sind. Die Kunststoffe, die insbesondere in der Luftfahrt, aber auch im Automobilbau angewendet werden, sind sehr schwer zu verkleben. Die haben eine bestimmte Oberflächenbeschaffenheit. Und die chemische Zusammensetzung der Oberfläche ist ungünstig für die meistgenutzten Klebstoffe und es muss eine sehr aufwendige Oberflächenbehandlung angewendet werden in den Teilen, die geklebt werden und das ist nur manchmal möglich bei manchen Kunststoffmatrizen bei Verbundwerkstoffen. Weil sie chemisch sehr schlecht mit den Klebstoffen interagieren. Dann können Sie sich fragen: Ok, dann bohrt man so eine Durchbohrung und verbindet sie mit einer Niete oder einem Bolzen. Aber dann hat man auf der einen Seite zusätzliches Gewicht durch das Verbindungselement selbst. Das ist nicht zu unterschätzen. So ein Airbus 380 hat über eine Million Nieten in der Struktur. Und die Nieten und Bolzen wiegen zwischen 15 Gramm und 30 Gramm. Und das ist schon relevant in der Luftfahrt. Jedes Kilo, jedes Gramm zählt in den Flugzeugen. Und am Anfang der 2000er war in der Fertigungscommunity wirklich die Notwendigkeit neue Fügeverfahren bzw. später, jetzt am Ende der 2000er und Anfang der 2010er Jahre auch im Bereich der additiven Fertigung eine Frage als Forschungsschwerpunkt ein neues Verfahren für die bessere Verbindung zwischen Kunststoffen und Metallen zu entwickeln. Das ist der Trend: Fügeverfahren, die eine geringere Wärmeentwicklung verursachen und die Festigkeit der Verbindung trotzdem so hoch hält oder verbessert sogar im Vergleich zu Klebstoffen und auch im Vergleich zu traditionellen Verbindungselementen wie Nieten oder Bolzen. Und das ist dann unser Ansatz gewesen, solche energieeffizienten Fertigungsverfahren, also Fügeverfahren und additive Fertigungsansätze, zu entwickeln, damit man am Ende eine festere Verbindung erreicht, die vielleicht auch nachhaltiger ist. Weniger Energie bedeutet, auch für die Umwelt etwas Gutes zu tun. Das ist, woran wir an der TU Graz weiter forschen.
Welche Möglichkeiten haben Sie jetzt? Sie haben sehr viele Patente bereits in Ihrem Forschungsleben erteilt bekommen. Welche Möglichkeiten und welche Verfahren haben Sie bereits entwickelt und entwickeln Sie auch gerade?
Amancio: Wir haben mehrere Patente für verschiedene Fügeverfahren und ein additives Fertigungsverfahren zurzeit. Das sind so, wenn ich mich nicht irre, fünf oder sechs Technologien, die wir patentiert haben in den letzten zehn bis fünfzehn Jahren, die sich zurzeit in verschiedenen Entwicklungsstadien befinden. Wir arbeiten mit einer Variante des Schweißverfahrens, dem sogenannten Festphase-Fügeverfahren. Das sind Verfahren, die die Schmelztemperatur des Metalls nie erreichen. Das heißt, wir arbeiten mit niedrigen Temperaturen, aber das Metall wird teigartig weich, aber nicht geschmolzen, nicht 100 Prozent flüssig. Aber ganz nahe – 80 bis 90 Prozent der Schmelzpunkttemperatur wird schon erreicht bei der Legierung. Und diese sogenannten Festphase-Fügeverfahren sind Fügeverfahren, die eine mechanische Schwingung, eine mechanische Bewegung, eine mechanische Energie, das heißt eine Arbeit, in Wärme transformieren. Wir reden grundsätzlich über reibebasierte Fügeverfahren. Das heißt, wir kreieren Wärme durch die Reibung zwischen den beiden Bauteilen. Oder durch die Nutzung von einem externen Werkzeug, die dann gegen das Bauteil reibt und es lokal erwärmt. Da ist dann der Schwerpunkt gewesen, dass es eine Technologie gibt, die Anfang der 90er-Jahre entwickelt worden ist in England bei TWI, das sogenannte Friction Stir Welding. Auf Deutsch: Rührreibschweißen. Und das ist dann, sagen wir, die Inspiration von meiner Arbeit gewesen. Und aus dieser Technologie wurde eine für Metall entwickelt. Insbesondere für Aluminiumschweißnähte, für Aluminiumbleche. Und da habe ich die Idee, dieses Verfahren als Inspiration für die Verbindung von hybriden Bauteilen, also Metallen und Kunststoffen. Und daraus habe ich mehrere Verfahren entwickelt, die auf dem Prinzip des Rührreibschweißens basierend gedacht worden sind – mit Reibung Wärme zu generieren, um diese Verbindung thermisch und materialstofflich auch zu verbinden.
Geht das dann in die Richtung des Ultraschallfügens oder ist das das Friction Riveting?
Amancio: Genau. Wir haben mehrere Verfahren für verschiedene Anwendungen. Wir haben ein Verfahren, das wir hier an der TU Graz schon seit 2018 weiterentwickelt haben und untersucht haben. Das sogenannte Friction Riveting. Das Friction Riveting, das Reibnieten, ist ein Verfahren, das doch mit einem metallischen Verbinder arbeitet. Aber mit einem kleineren Verbinder. Mit einem metallischen Verbinder einerseits, aber das Verfahren verlangt keinen Einsatz von einer Durchbohrung. Das heißt, die Niete wird eingesetzt direkt in dem Bauteil, es perforiert das Bauteil und kreiert schon die mechanische Veränderung direkt am Bauteil ohne es zu durchbohren, ohne es zu durchdringen. Es gibt da mehrere Vorteile: Natürlich sind Durchbohrungen Stresskonzentratoren und anfällig für Rissbildungen und Risswachstum. Wenn wir dann eines der Bauteile nicht komplett durchdringen, dann erhöhen wir die Schadenstoleranz der gesamten Struktur. Wenn wir keine Bohrung im Vorfeld, bevor die Niete eingesetzt wird, anstellen müssen, dann sind wir auch schneller mit kurzen Fertigungszeiten. Das sind die Vorteile dieser Technologie. Das ist ein Nietverfahren.
Wir haben aber auch andere Fügeverfahren, wie das Friction Spot Joining, die keine metallischen Nieten oder Elemente oder Klebstoffe nutzen. Und das ist ein Verfahren, wo wir dann, wie das Wort sagt, eine Punktschweiß- oder Punktverbindung herstellen. Ich vermeide, wie Sie wissen, das Wort Schweißen, weil man beim Schweißen davon ausgeht, dass eine Diffusion entweder auf atomarer oder molekularer Ebene stattfindet. Und bei Metall-Kunststoff-Verbundwerkstoffen findet keine große atomare oder molekulare Diffusion statt. Und deswegen sage ich Verbindung und keine Schweißung. Aber am Ende ist es eine Verbindung, eine Struktur, die gefügt wird. Und dieses Verfahren nutzt ein Werkzeug, dass aus zwei Teilen besteht. Und dieses Werkzeug durchdringt dann lokal das Material und generiert dann Hitze bei Reibung. Und gleichzeitig formt es lokal das Blech, das Metallbauteil leicht um und man hat dann am Ende eine Verbindung, die aus einer Mischung von mikromechanischen Veränderungen des Metalls im Kunststoff und die Konsolidierung des Kunststoffes in der Übergangszone durch die Reibung erwärmt worden ist und als eine Art Klebstoff agiert. Aber ohne den Zusatz von Klebstoff. Von der gleichen Matrix des Materials hat man dann die Entstehung von Attraktionskraft. Das heißt, es ist ein Verfahren, das grundsätzlich den Klebstoff ersetzt in der Anwendung der Leichtbaustruktur.
Dann haben wir auch ein anderes Verfahren, wo wir Ultraschall als Energie, als Schwingungsenergie nutzen. Das Ultraschallfügen ist auch ein Reibschweißverfahren, weil eben eine sogenannte Sonotrode, das Schweißwerkzeug oder Fügewerkzeug, vibriert ein Bauteil. Es ist in Kontakt mit einem der Bauteile. Man muss sich eine Überlappverbindung vorstellen mit zwei Bauteilen, die aufeinandergelegt werden und das Werkzeug, das Ultraschallfügewerkzeug, vibriert das obere Teil gegen das untere Bauteil und in der Übergangszone entsteht dann die Hitze durch die Reibung. Und weil man schneller Hitze erzeugt durch Reibung als das die Hitze weggezogen wird durch Wärmezufuhr, also Konvektion oder Konduktion oder Leitung, dass man dann die Temperatur in diesen Übergangszonen erhöht und dadurch dann die Matrix des Kunststoffes auch aufschmilzt oder auch aufweicht. Und so gibt es wieder die Benetzung des Metalls durch den aufgeschmolzenen Kunststoff. Dazu, in diesem Verfahren, das wir extra patentiert haben, ist die Einbringung von Mikrosäulen oder Pins in der Oberfläche des Metalls. Und diese Pins agieren oder die verbessern dann die Transformation von mechanischer Schwingung auf Wärmeenergie durch die Reibung. Das sind sogenannte Energy Directors. Sie führen die Vibration in der Spitze von diesen Elementen, die so wie in einer Haarbürste werden: Die Bürste sind die Pins und diese Pins werden dann auf die Oberfläche des Kunststoffes gerieben mit Ultraschallfrequenz – also sehr schnell. In der Spitze von diesen Pins gibt es eine Hitzeentwicklung und die dringen dann in den Kunststoff, als ob man eine Haarbürste in eine Knetmasse drückt. Wenn man schon als Kind so etwas gemacht hat, und hat dann später versucht, die Knetmasse von der Haarbürste zu trennen, weiß man, dass das sehr schwer ist. Und dann kommt die zweite Funktion von diesen Pins, die wir in die Oberfläche des Metalls integrieren. Das ist dann die Erhöhung der Schadenstoleranz der gesamten Struktur. Weil diese Pins sind mechanisch verankert. Wenn der Kunststoff konsolidiert, dann sind sie fest drinnen im Kunststoff. Das erhöht dann die Schadenstoleranz. Das bedeutet, dass wenn ein Riss entsteht zwischen diesen zwei Teilen – also dem Metall und dem Kunststoff – diese Pins brechen dann langsam, sukzessiv. Und der Risswachstum wird entschleunigt und die Struktur kann besser halten und kein katastrophaler Fehler findet statt. So kann man das ganz gut kontrollieren, wenn zum Beispiel das Flugzeug in Wartung ist am Boden kann man das dann sehr gut untersuchen mit nicht-destruktiven Methoden, wie zum Beispiel auch Ultraschall oder anderen Verfahren – dem sogenannten NDT-Verfahren. Das sind dann die Sachen, die wir entwickelt haben.
Ganz am Anfang waren wir bei der Herstellung des Kunststoffs und Metalls durch traditionelle Verfahren. Das heißt, wir haben einfach mit konventionellen Blechen gearbeitet. Oder dann Material genommen, und die Pins auf der Oberfläche gefräst. Das war aber eine Phase wo wir nur die Machbarkeit einer solchen Technologie gezeigt haben. Heute sind wir schon dabei, die additive Fertigung und den 3D-Druck zu nutzen. Zum Beispiel werden diese Pins dann topologisch optimiert. Das heißt, sie bekommen eine Form, wo die ganze Struktur weniger Material verlangt und leichter ist. Aber sie verlieren die Strukturfunktion nicht durch das Wegnehmen von Masse aus dem Metallbauteil. Und das kann man sehr gut durch das 3D-Drucken erreichen: Solche komplexen Strukturen, die topologisch optimiert werden kann man nur durch das 3D-Drucken erreichen und nicht zum Beispiel durch Fräsen in der Regel. Und bei Kunststoffen können wir auch das Gleiche machen oder bei Verbundwerkstoffen. Es gibt additive Fertigungsverfahren, mit denen wir auch kontinuierlich verstärkte Kunststoffe drucken können mittlerweile. Und deswegen wird es jetzt in diese Richtung gehen. Wir können zwei verschiedene Materialien oder Bauteile herstellen durch den 3D-Druck, die topologisch optimiert und leichter sind. Und dann eine zweite Fügetechnik nutzen, um diese zwei Bauteile zusammen zu fügen. Das ist ein Ansatz, der aktuell in Richtung Fügetechnik geht bei uns.
Wir haben aber seit 2015 noch aus meiner Zeit, als ich noch in Deutschland gearbeitet habe, eine Technologie entwickelt – das AddJoining. Das ist wirklich ein 3D-Druckverfahren. Das heißt, wir nehmen ein 3D-Druckverfahren für den Kunststoff und nutzen es, um ein metallisches Bauteil zu hybridisieren. Das heißt, wir drucken Kunststoff oder Verbundwerkstoff direkt auf eine metallische Oberfläche und dadurch können wir zum Beispiel Sensoren in den Kunststoffbauteilen integrieren oder Coatings in der Oberfläche aus Kunststoffen in den Metallbauteilen integrieren. Oder wirklich einmal sehr feste Übergansverbindungen zwischen großen Strukturen aus Kunststoff und aus Metall. Wie zum Beispiel der Rumpf ist in der Regel aus CFK. Aber die Verstärkung, die sogenannten Stringers sind aus Metall. Und wenn wir zum Beispiel die Struktur aus dem Rumpf direkt durch ein 3D-Druckverfahren in das Metallbauteil integrieren könnten auf eine optimale Art und Weise, dann können wir in Zukunft komplexe Bauteile bauen, die gleichzeitig leichter sind, in einem Verfahren oder mit weniger Schritten herstellen und ohne Nieten. Das heißt, es ist eine Evolution. Die Technologien, die wir an der TU Graz entwickelt haben und weiterentwickelt haben und zurzeit weiterentwickeln, haben alle ihre Nischenanwendungen. Sie sind keine Competitors, sie kämpfen nicht für die gleiche Anwendung, sondern sie sind geeignet für bestimmte Anwendungen, bestimmte Nischen. Und das macht sie interessant, das untersuchen wir im Rahmen von verschiedenen Industrieprojekten sowie akademischen Projekten im Institut für Werkstoffkunde, Fügetechnik und Umformtechnik und insbesondere in der Stiftungsprofessur für Luftfahrt.
Ich bin ein bisschen an dem Thema hängen geblieben, dass die Oberflächenstrukturen optimiert werden. Wie schaut das dann aus? Wie muss ich mir das ungefähr vorstellen?
Amancio: Sie meinen beim Ultraschallfügen? Sie sind wie Pins in der Oberfläche oder wie Zacken in der Haarbürste. Das sind dann kleine Pins, die können zylindrisch sein oder haben in der Regel einen Kopf mit einem breiteren Durchmesser – so wie ein Pilz zum Beispiel. Oder aber wenn wir in den Mikrobereich gehen – so 180, 200 Mikrometer und unter 200 Mikrometer – dann können wir zum Beispiel biomimetisch oder naturinspirierte Strukturen herstellen, wie die Gecko-Fuß-Strukturen. Der Gecko hat so bestimmte Mikrosäulen in dem Fuß, wenn man es mit einem Rasterelektronenmikroskop ansehen würde, man kann das nicht gut in einem optischen Mikroskop auflösen, sondern man braucht ein Rasterelektronenmikroskop. Da sieht man so kleine Pilze. Und diese sind dann flexibel und adaptieren sich auf die Oberfläche, wo sie dann sein wollen. Und die Verbindung kann wirklich sehr fest sein, deswegen fallen sie auch nicht ab, sogar, wenn sie am Dach sind. Und davon wollen wir uns auch inspirieren lassen, solche Strukturen in unseren Metallbauteilen zu drucken, bevor wir dann mit dem AddJoining-Verfahren diese Bauteile hybridisieren, damit wir solche komplexen mikrometrischen Strukturen erreichen, da müssen wir das 3D-Druckverfahren, das so genannte Laser Powder Bed Fusion, das sogenannte Selective Laser Melting auf Deutsch nutzen, das uns ermöglicht, solche Details, solche Strukturen direkt während des Druckverfahrens, das heißt, während der Fertigung der Bauteile in die Oberfläche, integrieren können.
Sie haben jetzt den Gecko als Inspiration genannt. Wo kommen denn Ihre Ideen her?
Amancio: Mittlerweile bin ich nicht alleine bei der Idee. Ich habe, muss man schon sagen, eine super Mannschaft, die zusammen mit mir arbeitet. Und die Ideen kommen nicht nur von mir, sondern auch von meinen Mitarbeitern und Mitarbeiterinnen. Bei den meisten dieser Fertigungsverfahren war ich damals Dissertant und danach Postdoc, als diese entstanden sind. Ich glaube, ich war damals sehr neugierig. Also, diese Problematik zu lösen, dass Metall schwer mit Kunststoff zu schweißen war. Und ich hatte dann nach neuen Ansätzen gesucht und gar nichts gefunden. Ich habe dann aber Schweißverfahren beobachtet, von denen vielleicht so das Prinzip doch für meine Anwendung anzuwenden wäre. Und da habe ich einmal ein bisschen gebastelt, getestet und immer versucht, die Materialkundekenntnisse anzuwenden, um zu verstehen, was das Verfahren auf den Verbindungsaufbau verursacht hat. Beziehungsweise, dann auf die mechanischen Eigenschaften und die Struktur solcher Verbindungen. Und beim Lesen, bei Versuchen, beim Ausprobieren und beim Testen kommen die Ideen. Und natürlich, wenn man mittlerweile von über 20 Patente spricht, da hatte ich vielleicht 150 Ideen ausprobiert, bis es zu diesen 22 Patenten kam. Es gibt keine Magie (lacht). Es gibt nur harte Arbeit.
Gerade in der Luftfahrt ist ja das Thema Sicherheit auch immer ein sehr, sehr wichtiges. Wenn man sich neue Verfahren anschaut, wie sicher sind sie im Gegensatz zu den klassischen oder herkömmlichen Verfahren?
Amancio: Gott sei Dank gibt es eine sehr strenge Sicherheitskontrolle bei allen einzelnen Entwicklungsphasen. Sei es bei neuen Materialien oder bei neuen Fertigungsverfahren. Das ist nicht so einfach, ein neues Fertigungsverfahren zu zertifizieren. Insbesondere in der Zivilluftfahrt. Bei Militäranwendungen ist es anders, weil die Ansprüche anders sind. Sagen wir so: Man hat andere Gegebenheiten als in der Zivilluftfahrt, wo das Leben von ein paar hundert Personen aufs Spiel gesetzt wird. In einem Militärflugzeug sind es ein paar Leute oder vielleicht nur ein Pilot, der sich jederzeit mit einem Parachute aus dem Flugzeug retten kann. Es gibt in der Zivilluftfahrt das sogenannte Building Block-Schema. Das heißt, dass bei jedem neuen Material oder einem neuen Fertigungsverfahren man an der Basis dieser Pyramide anfängt – so muss man sich das vorstellen. Und am Boden ist die erste Zertifizierungsebene, wo man nur auf der Probenebene arbeitet. Und alle Tests sind auf dieser Probenebene durchgeführt, bis dann die Zertifizierung und alle Sicherheit sichergestellt worden ist. Und dann geht es um den nächsten Schritt, wo dann kleine Demonstratoren-Bauteile hergestellt werden. Und dann werden alle auf dieser Ebene geprüft, bis das angezielte Sicherheitsniveau erreicht wird. Dann geht es weiter nach oben in Richtung der Spitze der Pyramide. Bis zum letzten Stadium, das dann schon das gesamte Flugzeug ist. Das ist das Fullscale Testing, das gesamte Flugzeug oder vielleicht so Teile des Flugzeuges – zum Beispiel die Tragfläche – als Ganzes wirklich einmal getestet wird, bis man dann auf dieser Ebene eine volle Zertifizierung erreicht. Dies Pyramide basiert auf den Technology Readiness Level. Wenn man so vergleichen würde: 0 ist die Basis der Pyramide und 9 – das ist das Maximum – ist die Spitze der Pyramide. Wir arbeiten an der TU Graz bis TRL 5. Das heißt, wir untersuchen auf der Probenebene bis zum Demonstratoren-Bauteil. Also Teilkomponenten zum Beispiel. Oder Komponenten, die auf Skala hergestellt werden. Weil unsere Expertise hier nicht in der Entwicklung von Flugzeugstrukturen liegt, sondern auf der Material- und der Fertigungstechnologie. Was darüber geht ist bei unseren Industriepartnern, die wirklich die Technologien, die wir ihnen transferieren, in wirkliche Strukturen umbauen und testen. Und dann gehen sie zum Zertifizierungsverfahren. Von diesen fünf bis sechs Technologien, die ich erwähnt habe, sind manche Technologien weiter – manche TRL 5 oder sogar 6 – und manche sind noch TRL 2 oder 3. Also in frühen Entwicklungsstadien. Und das Friction Spot Joining ist schon bei 5 oder 6. Da wurde schon demonstriert in wirklich großen Komponenten. Das Reibnieten ist auch 5 oder 6. Das Ultraschallfügen ist zwischen 3 und 4. Und das AddJoining, das ist das 3D-Druckverfahren für die hybriden Verbindungen, ist auch zwischen 3 und 4. So ist das Niveau von solchen Technologien für hybride Bauteile. Wir haben aber auch in den letzten drei Jahren total neue Fügetechnik hier an der TU Graz entwickelt für andere Arten von Mischverbindungen. Die basieren auch teilweise auf Reibenergie und anderen 3D-Druckverfahren. Ich darf aber im Moment noch nicht viel darüber sprechen – hoffentlich bald, wenn die Erfindungsmeldung als Patent angemeldet wird. Aber wir sind in Richtung Mischverbindung zwischen Metall und Holz, Holz und Verbundwerkstoff gegangen. Weil Holz ein sehr interessantes Material ist, das Verbundwerkstoffe auf Basis von Öl-Resigns oder Öl-Harzen ersetzen kann. Und dann ist die Herausforderung noch größer, weil Metall mit Holz kann man gut mit einem Nagel vernageln oder mit Schrauben arbeiten. Kleben geht teilweise, aber nicht wirklich in Anwendungen mit hohen Ansprüchen, wie in der Transportindustrie.
Aber da kann man mit Holz arbeiten?
Amancio: Ja, kann man. Man kann Holz auch schweißen. Durch Reibung. In diese Richtung geht man.
Sie sind aus Brasilien. Sie sind dann nach Deutschland, haben dort sehr lange gearbeitet, Ihr Doktorat fertiggemacht, waren dann auch Junior-Professor in Deutschland und sind jetzt an der TU Graz in der Stiftungsprofessur. Wie hat sich dieser Weg für Sie gestaltet? Wie ist es dazu gekommen? Was hat Sie schlussendlich nach Graz gebracht?
Amancio: Ich war knapp 18 Jahre in Deutschland. Ich war erstens als Masterstudent dort, aus Brasilien, aus Santo Andre gewechselt. Und dann habe ich meine Promotionsarbeit auch in Hamburg, an der TU Hamburg gemacht, habe dann eine Zeit lang als Wissenschafter, Postdoc und danach als Senior-Wissenschafter in einem Helmholtz-Zentrum Geesthacht gearbeitet. Und dann habe ich einen Nachwuchsgruppen-Grant bekommen. Das ist ähnlich wie ein CD-Labor in Deutschland – die Helmholtz-Nachwuchsgruppen zwischen dem Helmholtz-Zentrum in Geesthacht und der Technischen Universität in Hamburg. Und dort wurde ich parallel auch Junior-Professor. Junior-Professor ist ähnlich wie ein Assistant Professor in Österreich, mit dem Unterschied, dass ein Junior-Professor seine Dissertant*innen akademisch und wissenschaftlich selbst betreuen kann. Ein Assistant Professor in der Phase der Habilitation darf offiziell keine eigenen Dissertant*innen akademisch betreuen. Das war schon eine gute Sache für mich, der immer die akademische Laufbahn verfolgen wollte. Die Junior-Professur ist auch auf sechs Jahre begrenzt. Danach wird entweder entfristet oder man geht in Richtung anderer Stellen. In meinem Fall war es so: Meine Junior-Professur war zwar befristet, ich hätte aber am Ende eine sichere Stelle als Senior-Wissenschafter in diesem Helmholtz-Zentrum gehabt, wenn ich eine positive Beurteilung über meine Junior-Professor bekommen hätte. Das war der Fall. Aber es gab keine Perspektive, mich im akademischen Bereich weiter zu entwickeln. Und dann war für mich klar, dass es zwar als Senior-Wissenschafter schön wäre, ich aber mehr wollte für die Karriere. Und dann habe ich mich angefangen, bei verschiedenen Stellen zu bewerben. In Deutschland, in den USA, in Holland und hier in Graz. Aber gezielt. Und ich kannte die TU Graz schon. Die TU Graz hat einen sehr guten Ruf im deutschsprachigen Raum und auch international im Bereich Werkstoffkunde. Und auch im Bereich Fügetechnik. Und war für mich sehr attraktiv, wegen meines Know-How aus Deutschland – weil in Deutschland habe ich immer mit Luftfahrt-Materialien gearbeitet und Fügetechnik und das hat sehr gut gepasst. Und für die Stellen, für die ich mich beworben hatte, war diese für mich am attraktivsten aus dieser Auswahl. Weil auch eben dabei durch diese Stiftungsprofessur wir eine sehr gute Ausstattung für eine neue Arbeitsgruppe hatten. Das war schon ausschlaggebend, dass ich nach Graz gekommen bin. Und wir sind auch in einer schönen Region hier muss man sagen. Graz ist wunderschön. Nicht, dass Hamburg und Umgebung nicht schön sind, aber wettermäßig ist Graz besser für einen Brasilianer, würde ich sagen (lacht).
Das Hauptthema unserer diesmaligen Staffel ist ja auch die smarte Produktion. Was ist für Sie smarte Produktion und gehört Ihr Forschungsgebiet dort hinein?
Amancio: Ja genau. Wobei ich kein Fachexperte bin in Smart Production. In Deutschland wird Smart Production als Synonym für Industrie 4.0 genannt. In Österreich nutzt man gerne den Begriff Smart Production. Da haben Kollegen beim Institut für Fertigungstechnik die bessere Expertise. Aber für mich als Ingenieur ist meine Interpretation der Smart Production, dass man, um eine Smart Production zu erreichen, einen Ausgleich zwischen dem Human-Faktor und dem Maschinen-Faktor schaffen muss. Beim Maschinen-Faktor spielt sicherlich die künstliche Intelligenz, insbesondere Big Data und Machine Learning, eine wichtige Rolle. Nicht nur das, weil ohne das geeignete Fertigungsverfahren bringt Automatisierung oder Digitalisierung gar nichts. Und bis jetzt können künstliche Intelligenzen noch keine Fertigungsverfahren selbst auswählen. Die können Ergebnisse auswerten, daraus lernen, aber man muss es einem Menschen geben, der vernünftig das richtige Material und das richtige Fertigungsverfahren für die Maschine vorschlagen wird. Das heißt, das Human-Material ist für mich auch ein großer Bestandteil der Smart Production. Es mag andere Meinungen geben, dass irgendwann der Mensch weniger Einfluss haben wird, aber ich bin der Meinung, dass das nicht der Fall sein wird. Und deswegen versuche ich und auch unsere Kolleg*innen am Institut, unsere zukünftigen Ingenieure so auszubilden, mit dieser Mentalität. Und sie vorzubereiten. Sie müssen wirklich vorbereitet sein, sich mit der Digitalisierung auseinanderzusetzen, wenn sie im Arbeitsmarkt sind. Aber sie müssen die Grundlagen-Kenntnisse haben, und zwar in der Werkstoffkunde. Und zwar in der Festigkeit der Materialien, in der Fertigungstechnik, in der Oberflächentechnik. Und das kann eine Maschine noch nicht von selbst. Und deswegen ist für mich eine Smart Production eine Kombination von smarten Leuten und nachhaltigeren Fertigungsverfahren und die Nutzung von Robotisierung und künstlicher Intelligenz als Unterstützung für die Optimierung dieses Verfahrens.
Eine abschließende Frage habe ich noch: In der Forschung ist ja immer Geld und Finanzierung ein sehr großes Thema. Wenn es einmal kein Thema wäre, was würden Sie gerne umsetzen wollen?
Amancio: Das ist eine tolle Frage und man hofft, dass unser Rektor auch meine Antwort mithört (lacht). Das ist natürlich ein Witz. Aber es gibt natürlich auch eine Wahrheit dahinter. Geld ist natürlich sehr wichtig heute. Und insbesondere in meinem Bereich braucht man wirklich Hardware, braucht man Maschinen, Prototypen, die unsere Idee demonstrieren werden. Und wenn ich Geld hätte, wenn ich ausreichend Budget zur Verfügung hätte, dann würde ich einen nächsten Schritt gehen. Heute arbeiten wir mit adaptierten, kommerziellen Geräten. Meistens Desktop-Geräten, kleinen 3D-Druckern oder kompakten Schweißgeräten oder Fügegeräten, die für die Grundlagenforschung ausreichend sind, aber der nächste Schritt, der natürliche Schritt ist dann zum großen Technology Readiness Level zu gehen. Das heißt, wir brauchen Geräte, die größer sind, damit wir wirklich große Bauteile bauen können, wozu wir im Moment noch nicht in der Lage sind. Wir sind schon auf einem guten Weg, aber das wäre mein Traum und ich glaube eine gute Strategie für die TU Graz, damit wir auf die Hochskalierung gehen könnten. Das wäre eine Pilotfabrik. Aber dann können Sie sagen, dass es schon eine Pilotfabrik gibt. Unsere smartfactory. Allerdings arbeitet die smartfactory mit herkömmlichen Fertigungsgeräten. In meinem Fall muss ich sie selber entwickeln und selber bauen. Es gibt sie nicht off-the-shelf zu kaufen. Und deswegen, wenn Sie mir zehn Millionen geben würden wäre es super, wenn Sie mir fünf Millionen geben würden, dann wäre es ausreichend.
Vielen Dank für das Gespräch!
Amancio: Danke sehr! Ich bedanke mich.
Vielen Dank, dass Ihr heute wieder mit dabei wart! Wir hören uns beim nächsten Mal!