Circular Economy: Valuable Raw Materials from Waste
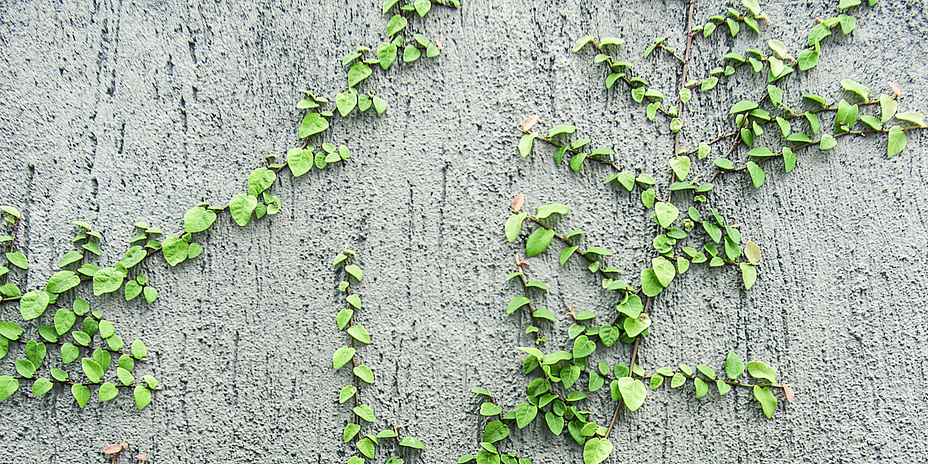
Concrete is still one of the most widely used building materials and an indispensable part of our urban environments. But its environmental footprint is significant, mainly due to the energy- and carbon-intensive cement that is typically used in the production process.
Concrete is actually a mixture of various ingredients. It contains stone of different degrees of coarseness, a binder (usually portland cement, or portland composite cement, where the portland cement clinker is mixed with additives) and, if necessary, other ingredients that can influence the properties of the concrete – making it particularly strong or durable, for instance. Adding water to this stone-binder mixture triggers a chemical reaction that causes the concrete to solidify.
Production of conventional cement involves sintering, which calls for very high temperatures. But the construction industry – and, in turn, cement manufacturing – will have to be transformed as part of ongoing efforts to transition to a more sustainable future. The same goes for iron and steel production, and granulated slag – a by-product of these processes – is already used as an additive in the manufacture of cement and concrete. However, as iron and steel producers adopt low-carbon or zero-carbon processes, supplies of granulated slag will drop significantly or disappear altogether in future, although other types of slag that are not currently suitable for use as binding components in conventional concrete will still be available. Now, researchers around the world are looking for alternatives.
UpcycSlag-Binder
Researchers from the Institute of Material Testing and Construction Materials Technology with affiliated research institute for strength and material testing, in collaboration with the University of Leoben, are aiming to identify such an alternative in the UpcycSlag-Binder project. The partners were recently nominated for the Energy Globe Award Styria in recognition of their work. The researchers have developed a new binding agent component made from blast furnace residues that has the same properties as granulated slag. The binder is also made from slag generated in the production of iron and steel, which currently either has to be disposed of or stored. In the development process, Joachim Juhart and his team at TU Graz were mainly responsible for identifying the structural properties that the new binder had to meet in order to be used in the construction industry. “Over the coming years, the steel and cement industries will undergo fundamental changes as they make the transition to fossil-fuel-free and zero-carbon production. This means waste products will become valuable raw materials, but the processes will have to be adapted. Today, the focus is on steel quality, but in future more attention will need to be paid to the quality of slag, while slag will also have to be processed in parallel with steel production,” Juhart explains.
The results of the project have been very promising, and a follow-up project, called Recover Met Binder, is currently in the pipeline.
CD Laboratory for waste-based geopolymer construction materials in the CO2-neutral circular economy
Cyrill Grengg and his team at the CD Laboratory for waste-based geopolymer construction materials in the CO2-neutral circular economy are moving in a similar direction, but taking a somewhat different path. They have used mineral residues and wastes as the basis for completely new construction materials, which could replace conventional cement-based concrete. Materials for applications that are susceptible to corrosion, such as sewerage systems and biowaste plants, have particularly strong potential. They contain slag and ash, as well as mineral wools and clay-rich demolition waste, which are then mixed with other high-carbon materials, including waste oils, biomass and organic fibres, to produce a new geopolymer. “In chemical terms, the geopolymer is completely different to portland cement, but their physical properties are very similar, and in some cases those of the geopolymer are actually better,” says Cyrill Grengg, head of the CD Laboratory. The lab will conduct research with eight corporate partners over the next seven years.
Read more about sustainable concrete in the dossier "Sustainable Construction with Concrete".
Kontakt
Joachim JUHART
Dipl.-Ing. Dr.techn.
Institut für Materialprüfung und Baustofftechnologie mit TVFA
Tel.: +43 316 873 7161
joachim.juhart @tugraz.at