TU Graz and AVL launch Battery Safety Center Graz
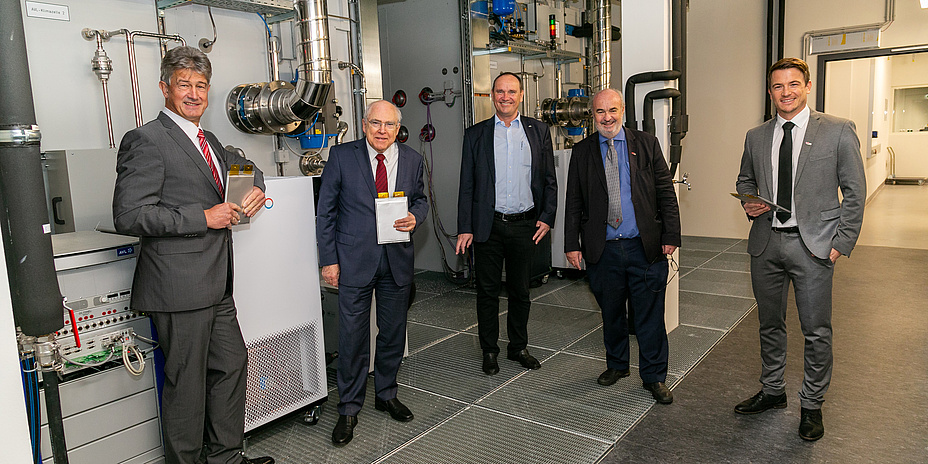
The declared aim of the Battery Safety Center Graz is to guide batteries for electric vehicles specifically to their load limits and to generate valuable data on the safety of future electric energy storage systems. The focus of the new research facility at Graz University of Technology is on two topics: the defined ageing of batteries for the analysis of long-term behaviour and the behaviour of charged batteries under mechanical stress in general and in the case of accidents in particular. The innovative testing possibilities under laboratory conditions make the centre a unique research facility of its kind in Europe. The research centre on Campus Inffeldgasse will be officially opened next year, when all test rigs have been finalized and are ready for use. The first insights into the new research infrastructure were revealed today, October 16th 2020, to a group of people from inside TU Graz and AVL as well as media representatives.
For high-quality research and future-oriented teaching
With the Battery Safety Center Graz, TU Graz now has access to state-of-the-art test bench technology for demanding research projects and future-oriented teaching in the field of battery safety. The major part of the test infrastructure as well as the building infrastructure itself comes from TU Graz, while AVL is involved in the cooperation with three climate chambers for electro-thermal tests. In total, both cooperation partners have invested almost 9 million euros, 5 million euros of which alone for the construction and basic infrastructure.
TU Graz Rector Harald Kainz welcomes the investment in the future field of battery safety and is delighted about the close cooperation with AVL: "With the Battery Safety Center Graz, TU Graz and AVL once again combine their scientific and technological competence and jointly demonstrate their international strength in the field of battery safety."
Helmut List, CEO AVL, explains his company's intentions: “The development of batteries is becoming more and more complex due to the constantly increasing requirements. This makes battery safety all the more important, and we are making a significant contribution to it through cooperation in the areas of testing and research, such as with the Battery Safety Center Graz, which we have presented together with Graz University of Technology. The testing technology used here is also state-of-the-art and is used globally by AVL and our customers in the same form."
Robert Fischer, managing director of engineering and technology drive systems of AVL List GmbH, adds: "The valuable research partnership between industry and university is demonstrated by existing cooperation projects, as the example of the AVL-TU Graz Transmission Center demonstrate. And now, AVL is also intensifying its cooperation with the Battery Safety Center Graz at the Vehicle Safety Institute, with which AVL is already working on a forward-looking project. "SafeBattery" focuses on topics of crash safety of high-voltage energy storage systems as an integral subsystem in the complete vehicle."
Hermann Steffan, head of the Institute of Vehicle Safety at TU Graz, also emphasizes "that we at the Institute of Vehicle Safety focus on both teaching and research into safety aspects of battery systems for vehicle drives. The test environments of the Battery Safety Center Graz open up new possibilities in teaching, where we can familiarize our students at an early stage with highly innovative test and analysis procedures related to battery safety. An immense advantage for the students themselves, but also for their future employers."
Hot-cold for batteries
The Battery Safety Center Graz offers a total of 550 square meters of laboratory space with a technical environment which includes an electro-thermal and a mechanical test environment. AVL contributes three identical climate chambers, each with almost 17 cubic meters for electrical battery tests, to the electro-thermal test environment. Jörg Moser from the Institute of Vehicle Safety and head of the new research centre explains: "In the climate chambers we can put battery systems through their paces during the charging and discharging process. From minus 40 to plus 90 degrees Celsius. We can age the batteries in a targeted manner by means of individually programmable cycles and receive detailed information for analysing battery performance. This would be very difficult or even impossible to achieve under normal conditions during test drives." A salient point here is the parallel operation of the three climate chambers. This means that the energy from the discharge process in one chamber can be used simultaneously to charge a battery in another chamber – a major contribution to more sustainable and resource-saving battery research.
About half of the capacity of the climate chambers is earmarked for joint projects between TU Graz and AVL. The other half is available to TU Graz for its own research purposes, teaching and research projects with other cooperation partners.
Crash system for battery tests
In addition to the climate chambers, the Battery Safety Center Graz offers completely new mechanical test facilities, including a highly dynamic crash system for charged batteries developed at the Institute. Two test variants can be run at a maximum speed of more than 100 km/h over a length of almost 20 metres. First, with a battery mounted on the test sled, which is highly accelerated and then braked, and thus exposed to forces of up to three hundred times the weight of the battery. And secondly, with a battery attached to the crash block, which is hit in a targeted manner by an impactor (which is a fixed geometric shape such as a cylinder or a sphere) mounted on the test trolley.
The safety equipment for the entire crash area was also developed at the Institute itself. It consists of a crash block weighing 150 tons and decoupled from the building with an integrated ventilation system. Special sensors record all relevant data on the condition of the battery during a test period, which in some cases is only a few milliseconds. Several high-speed cameras as well as a specially designed lighting technology provide high-resolution image and video material for detailed analysis of the battery system during the test.
For further mechanical stress tests, a hydraulic test stand called the "PRESTO 420" for quasi-static, i.e. extremely slow, and test speeds is available at the Battery Safety Center Graz, again designed by the Institute of Vehicle Safety at Graz University of Technology. Researchers are particularly interested in the sometimes very different behaviour of batteries due to the load speed. Charged and uncharged battery modules, battery cells and cell stacks can be subjected to a maximum compressive force of 420 kilo-Newton (which corresponds to a weight force of approximately 42 tons).
The "BATMAN" charging unit enables batteries to be charged and discharged quickly while simultaneously recording the temperature. The "ROBIN" is a clamping device for charging and discharging under controlled mechanical pre-stress. The test environment is completed by the "RIDDLER", a special battery workstation with integrated extraction and flooding system. Here, battery modules and cells are dismantled after being exposed to the stresses on the various test benches under the highest safety precautions and prepared for professional disposal.
Jörg Moser refers to the strict safety precautions of the Battery Safety Center Graz – even during construction: "This entire test environment is designed to stress batteries to the limit. Accordingly, we have attached great importance to fire protection, extinguishing and safety precautions and have also coordinated and tested these with various external experts, the professional fire brigade of Graz and the voluntary fire brigade of TU Graz."
Proven successful cooperation model
The Battery Safety Center Graz is the result of a long-standing cooperation between the Institute of Vehicle Safety at TU Graz and AVL List GmbH in the field of battery safety. The research cooperation was concluded for an indefinite period of time and is evaluated annually. The nature and scope of this new cooperation is similar to the "AVL-TU Graz Transmission Center", which started operations in 2017 as one of the world's leading transmission competence centres and is also located on Campus Inffeldgasse.
Kontakt
Media contact for TU Graz:
Barbara Gigler
Press officer TU Graz
Phone: +43 316 873 6006
Mob.: + 43 664 608736006
E-mail: barbara.gigler @tugraz.at
Media contact for AVL:
Michael KSELA
Company spokesman of AVL
Mobile: +43 664 132 81 78
E-Mail: michael.ksela @scoopandspoon.com