Getting the measure of tricky measurements
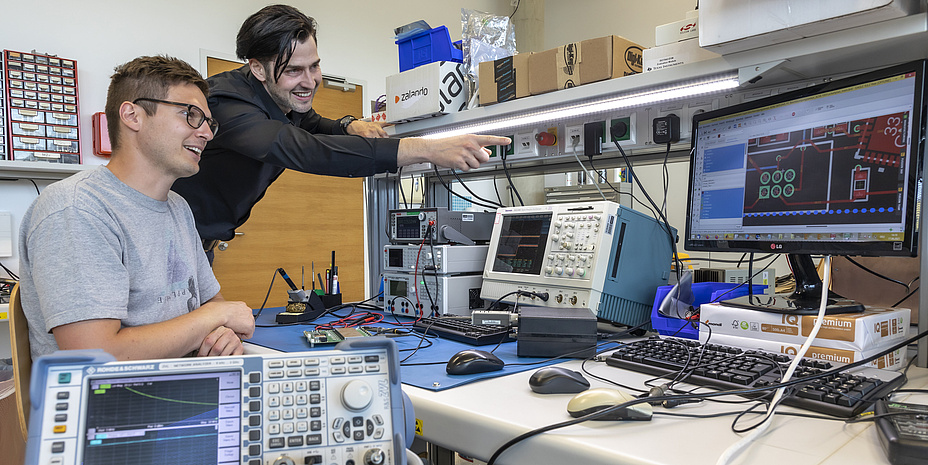
Although measurement technology has come a long way, established approaches often come up against their limits in difficult operating and environmental conditions, ultimately delivering inaccurate results or even none at all. Especially in the iron and steel industry, this is primarily due to a lack of (or a lack of suitable) sensor technology that can be used in the presence of dominant disruptive factors such as noise, electromagnetic radiation, heat, dust or ageing effects. A situation that the Christian Doppler (CD) Laboratory for Measurement Systems for Harsh Operating Conditions is looking to change. The newest CD Laboratory at TU Graz opened on 28 September 2021 with a ceremony attended by selected guests. Over the next seven years, the laboratory will carry out research into new measurement methods and systems, in collaboration with corporate partners voestalpine Stahl GmbH, voestalpine Stahl Donawitz GmbH and AVL.
The largest public-sector provider of funding for the laboratory is the Austrian Federal Ministry for Digital and Economic Affairs. "Our CD labs provide companies with a decisive competitive advantage. The scientists research enormously important parameters together with the corporate partners. With the ability to measure more precisely, safety margins could be reduced and thus processes made much more efficient. The consequences are savings in materials and emissions, a competitive advantage for companies and, at the same time, progress in protecting the climate and the environment," says Minister of Economics Margarete Schramböck.
From steel manufacturing to forecasts for battery ageing
The fundamental questions that will be addressed by the Christian Doppler Laboratory span a new line of research into measurement technology, which will be investigated in its entirety for the first time. The research focuses are flow measurement in pneumatic transportation processes (looking at the transportation of bulk goods through pipes and hoses by means of excess or low pressure), robust process measurement techniques in secondary metallurgy (an essential step designed to increase quality in steel production processes), sensors for improved flow control in continuous casting plants where liquid steel is cast to create an endless strand, as well as status monitoring for processing plants and forecasting the ageing of lithium-ion batteries.
“Our aim is not only to generate results that will feed into new measurement systems and sensor solutions for the benefit of our partners; we also want to improve our basic understanding of the causes of weak sensor signals and how to deal with them,” says Hannes Wegleiter, who will head the lab. The CD Laboratory is the product of years of preliminary work by Wegleiter and his Energy Aware Measurement Systems working group, which is based at TU Graz’s Institute of Electrical Measurement and Sensor Systems. Five doctoral students and two senior scientists will work on research questions at the laboratory.
This CD laboratory is anchored at TU Graz in the Field of Expertise "Information, Communication and Computing".
There are currently 13 active and opened CD laboratories at TU Graz:
- CD Laboratory for Measurement Systems for Harsh Operating Conditions
- CD Laboratory for Technology-Guided Electronic Component Design and Characterization
- CD Laboratory for Innovative Pichia Pastoris Host and Vector Systems
- CD Laboratory for Organocatalysis in Polymerization
- CD Laboratory for Location-Aware Electronic Systems
- CD Laboratory for Direct-Write Fabrication of 3D Nano-Probes
- CD Laboratory for Mass Transport through Paper
- CD Laboratory for Quality Assurance Methodologies for Autonomous Cyber-Physical Systems
- CD Laboratory for Design of High-Performance Alloys by Thermomechanical Processing
- CD Laboratory for Model-Based Control of Complex Test Bed Systems
- CD Laboratory for Pump and Fan Applications utilising Brushless Drives
- CD Laboratory for Fiber Swelling and Paper Performance
- CD Laboratory for Semantic 3D Computer Vision
Kontakt
Hannes WEGLEITER
Assoc.Prof. Dipl.-Ing. Dr.techn.
TU Graz | Institute of Electrical Measurement and Sensor Systems
Phone: +43 316 873 30512
wegleiter @tugraz.at